Now that we had both the hot room and the changing room all
insulated and cozy, it was time to start getting the hot room floor ready. The
installation instructions for the Kuuma wood burning stove call for the ceiling
to be protected with a non-combustible material having a 2 inch air gap. So, I
bought ½ inch Durock solid cement board for that purpose. The plan was to have
2 sheets of this stuff sandwiched together with a 2 inch space separating them.
We first took down measurements from the back wall to the chimney support box.
We then transferred those measurements on to our Durock and marked the support
box opening with a marker. For making the opening, the best tool I had was an
angle grinder. Actually worked out really well.
 |
Using an angle grinder to cut the Durock |
We then transferred the mirror image of the cutout on to the
2nd sheet. Make sure you have the unmarked side of the Durock board as
the visible side when you hang it up on the ceiling. Now that we had two pieces
all ready and cut, we needed to hang them. The first sheet goes up with just
2.5 inch non-rusting screws. Then, to make a 2 inch air space, we used scrap
pieces of the Durock as spacers. 4 ½ inch pieces make up 2 inches of spacing. For
those, we used 4 inch screws to attach the spacers to the joists in the ceiling.
The final piece of Durock will then go over the spacers with 4 inch screws.
 |
Durock over chimney support with spacers 1 |
 |
Durock over chimney support with spacers 2 |
Next step was to build a non-combustible pad for our stove
to stand on. The big box store has 12”x12” patio pavers that sit about 2” high.
I figured 6 of those would be perfect for this project. At under $2 each—this was
a great deal. A few things go in to laying the pad. You need to be sure the
stove sits on it in such a way that there’s a some slack behind the stove,
and that when you open the stove door, if any coals fall out, they fall on the
pad—not your floor. Also, you need to make sure that the chimney lines up with
the stove and the stove is center on the pad from left to right. Once all that
was calculated, the pavers then get glued to the floor with a high heat liquid
nails—PL400. One mistake I made is I didn’t apply any glue to the edges of the
paver—only the bottom. Applying glue to the edges will prevent water from
getting in the cracks between the pavers.
Because I intend to use the sauna to the fullest, I needed
the floor to have a drain. I found the best location where I could make all the
water run to and marked the spot. Next, I needed to give the floor a slope so
that any water from any sides would run down to the drain. To do that, I
learned from Glenn of
SaunaTimes.com that I need to build sleepers. Sleepers
are pieces of wood made in to triangles that start out for me at about 1.5 inch
thick at the walls and go down to nothing by the drain. Those can be cut using
a table saw. To decide how thick your sleepers should be, simply use a level.
The point at which the bubble goes out of level is where you sleeper height can
start. Make sure there’s not too much space between the sleepers so that the Durock
that will be sitting on top of them wont crack when people walk on it. I did
about 6-8 inch gaps. Once I laid all the sleepers out and they looked good, I
put down some liquid nails on the bottom side of each sleeper and nailed it to
the floor with brad nails.
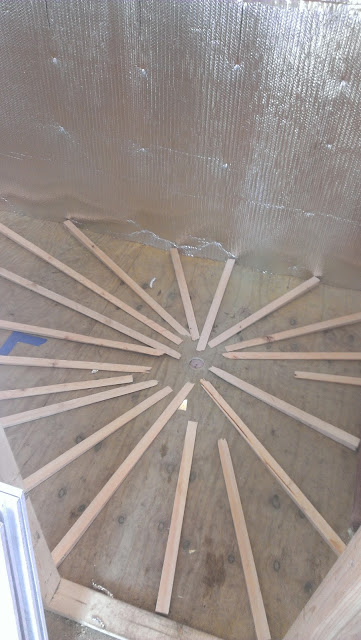 |
Sleepers create slope towards the drain. |
With all the sleepers attached we started putting down the Durock.
This stuff comes in sheets of 3x5 feet. I used the ½ “ thick ones. They’re
pretty strong yet still bend. Starting in one corner, I laid the first sheet
down, pre-drilled the holes through the sleepers and using exterior screws, attached
the sheet to the floor through the sleepers.
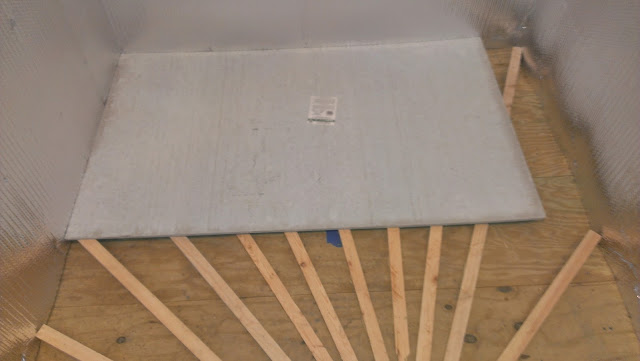 |
Setting the first floor sheet of Durock. |
I tested that the sheet can hold
my weight without any soft spots. If it was good, I’d do the next sheet. One
thing I learned here is they have special screws for Durock. The plus of those
screws is they drive in flush with the board. That way no sharp heads stick out
that can cut our waterproof rubber membrane that we’ll be putting on top later.
 |
Floor slope completed. View from one side. |
 |
Floor slope completed. View from the opposite side. |
Once all the Durock has been attached to the floor, you
should be able to see with a level, that the floor slopes down toward the drain
no matter where you put the level.
With the floor finally complete which took longer than I
wanted to, it was now ready to be waterproofed. There are different techniques
to do it. You could put RedGuard over the Durock. However, that needs temps of
like 50F+ for it to cure for 72 hrs—it’s the middle of winter now. You could
skim coat with cement, but that too requires certain temps and getting dirty.
The option I chose is a 40 mil rubber membrane used for waterproofing shower
pans. It sells at $5 per liner foot at 4 foot high pieces. So 4 feet x N-number
of feet you need x $5. It’s more expensive than skim coating, but cleaner and
quicker. Now the stuff you buy at the box store is PVC material. The other option
is CPE material which is more appropriate for a sauna, but is only available
online and is more expensive. If you have the money, that stuff is used for
radiant floors so it withstands like 600F heat. At the money I’m saving, I’m
willing to try the PVC stuff as I’ve seen some references to it being used in
saunas online. For 25 feet I paid around $100.
The way I used this material is the same way I did it when I
did my walk-in shower in the house basement. I started by rolling out my 12 foot
roll the long way the length of the sauna making sure I had even overhang on
both sides. Then, I took it up the wall about 6 inches on one of the long
sides. Using my leftover roofing nails, I nailed 1 inch from the top of the
membrane along the wall on every stud. So, in essence, I had half the floor
covered with the 4 foot piece and the corner where the wall meets the floor was
protected as well. Next I did the same thing on the opposite long wall. I left
the 2 short walls unattached as well as the seam in the middle. That was done
so that I had slack to install the drip edge along the floor perimeter. Stay
tuned for more in the next post.
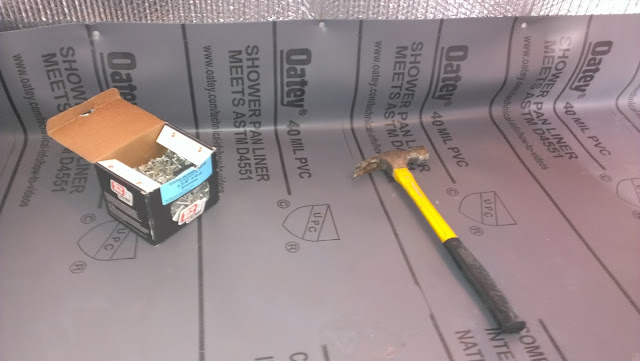 |
Waterproofing membrane going up the wall 6-8 inches. |
 |
Attaching the waterproofing membrane to the wall with roofing nails. |
 |
Waterproofing PVC membrane attached only on 2 opposite walls. |
I ran across your blog purely by accident. I really enjoyed reading about your well documented project that really goes into some great detail. I wish that I had the skills and the time to dedicate to building an outdoor sauna. Maybe, someday in the future. Keep up the good work buddy, I'll be keeping an eye on your project.
ReplyDeleteRonni Casillas @ JNH Life Styles
I'm getting ready to build a sauna this spring. Thanks for sharing your detailed steps. I see that some people skin the floor drain, but I'd rather have one so that I can be generous with rinsing myself and cleaning the sauna. The thing I can't figure out is where to send all of that water in the middle of the winter. I'm afraid the drain pipe will just freeze up...What's your thoughts?
ReplyDeleteThe floor does stay cold even in the hottest sauna days. Due to the incline of the landscape, my sauna is built on stilts so I have space under the floor. I only put in about a 1 foot length of 2" pipe for the drain. However, I don't have much water in the sauna aside from the occasional water fights :)
DeleteThanks for posting. This is super helpful. I am wondering if the rubber smell from the shower membrane dissipates after installation. We are planning on installing a floating cedar floor directly over the membrane and I'm a little concerned about the smell sticking around forever. What has your experience been?
ReplyDeleteHi! Originally, I only had the rubber membrane over the hot room floor with the click-in wood-like tiles from Ikea over it until the city inspector made me cover it with cement. I don't remember the smell ever being a problem. However, my sauna is up on posts so there's cold air circulating under the bottom of it and possibly kept the membrane cool enough that it didn't smell. Not sure how it acts if you heat it up. Btw, in the end, I was pretty happy that I cemented the floor. Less to worry about and very durable!
ReplyDelete